Scuff-Free Solution with Custom-Molded Material
Last updated on
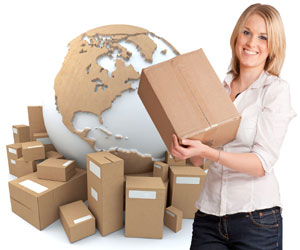
Sealed Air’s Packaging Design and Development Centers Provide Customers with Cost-Effective Solutions for Demanding Packaging Challenges
DANBURY, Conn. (Aug. 10, 2007) – Stern Pinball, Inc. – located in Melrose Park, Ill. – is the only coin-operated pinball manufacturer in the world. The company produces nearly 10,000 games a year. With that level of production, Stern Pinball makes customer service a number one priority.
In 2004, Joe Blackwell, director of customer service for Stern Pinball, took a call from a customer – who just happened to be Kevin Dabrowski, regional manager of Sealed Air’s Packaging Design and Development Center in Hodgkins, Ill. After Blackwell assisted Dabrowski with his pinball machine issue, Dabrowski turned the tables by offering suggestions about the packaging.
Stern had issues with aesthetic damage to its pinball machines. The corrugated boxes the company was using created scuff marks on the machines during shipment – tarnishing the pinball machines, in addition to Stern’s reputation. The company needed a new packaging solution to solve the scuffing problem, as well as reduce packaging cost, without sacrificing protection. Even with these damage issues, most of the decision makers in the organization were concerned about switching to a different packaging process.
“If I was approached in any other way, I wouldn’t have listened to Kevin Dabrowski’s suggestions,” stated Blackwell. “The phone call was the perfect customer experience.”
This motivated Blackwell to visit Sealed Air’s Packaging Design and Development Center in Illinois. “After I visited the center, I was completely impressed,” Blackwell continued. “The Sealed Air facility is over 100,000 square feet, and the staff was very helpful.”
Blackwell and Dabrowski immediately began discussing the carton design for packaging pinball machines. Since the standard carton size had to remain the same, the only changes that could be made were inside the box.
At Sealed Air’s Packaging Design and Development Center, Dabrowski introduced Blackwell to Instapak® GFlex® QS foam packaging. This unique foam formulation, in conjunction with the Sealed Air SpeedyPacker® foam-in-bag packaging system, would be the best solution to package a pinball machine of considerable weight and size. The highperformance foam packaging is resilient enough to hold up to the rigors of transporting a pinball machine around the world.
The SpeedyPacker® foam-in-bag packaging system is designed to dispense foam-filled bags in a variety of sizes. Once dispensed from the SpeedyPacker®, the foam inside the bag continues the expansion process and is placed in a simple mold to form custom-fit protective cushions. GFlex® high performance foam is specifically engineered to accommodate heavy products that require multiple impact protection during shipping. Additionally, the foam’s unique physical characteristics create high-performance cushions using minimal material, allowing for an overall reduction in package cube.
Blackwell supplied Dabrowski with a pinball machine and standard carton for Sealed Air design engineers to use in creating a trial packaging solution. When developing any packaging solution, Sealed Air engineers are challenged with providing a better way to package a product while reducing the amount of material and number of pieces, as well as the cost.
“We knew we would need to use cushions on each corner of the machine,” Dabrowski stated. “It was important for the customer to keep the cost down, so using small cushions on all corners of the machine was the best option for Stern because it offered the most protection with the least amount of material.”
The pinball machines were getting damaged during shipment because the detached legs of the machine went into paperboard tubes that ran the length of the machine. Vibrations during transport caused the tubes to scuff the machine. Dabrowski decided to notch out two of the cushions so the legs would be held securely in place away from the body of the machine – keeping the two objects from rubbing together and ultimately preventing abrasions.
Armed with a tape measure, pencil and legal pad of paper, Dabrowski got to work. After measuring each dimension, he built a prototype for each corner of the machine out of a block of wood. The dimensions of the shipping container minus the dimensions of the product gave Dabrowski an approximate thickness value available for each cushion.
Since both sides of a pinball machine are mirror images of each other, Dabrowski was able to create five cushions for one side of the machine, and then create a mirror image of those cushions for the other side. The entire process took about two days. On the second day, Dabrowski made a few minor changes and created a loading fixture to help Stern employees slide each machine horizontally into each carton.
Blackwell was not concerned with the machines getting damaged from being dropped, therefore the testing process for verification focused on vibration only. Blackwell and Dabrowski packaged two separate pinball machines – one with the old package design and the other with the new package design using Instapak® foam packaging. For two hours, each package went through a random vibration test at Sealed Air’s Packaging Design and Development Center to simulate conditions a packaged product might encounter during shipment.
After both packs were tested, they were pulled from their cartons. The pinball machine packaged in corrugated had blue streaks where the paperboard tubes had rubbed the surface of the machine. After two hours, there was enough abrasion to indicate the corrugated pack would continue to abrade the machine during longer shipments.
The pinball machine packaged with Instapak® foam packaging showed no signs of abrasion. The cushions were still in good condition, and the machine looked just as it did prior to the vibration testing.
After surviving the rigors of the vibration test, the new packaging design was then tested in the field. Blackwell shipped and tracked the condition of numerous machines. None of the pinball machines received damage – convincing Blackwell the Instapak® design was successful. A group of Sealed Air representatives spent the day at Stern, teaching and assisting with the packaging process and making suggestions to help increase speed and flow. The employees experienced a more streamline process than they had with the corrugated package design. They quickly understood the new design and loved it.
Also, the new solution required less storage space than all the corrugated materials. Only three SKU’s are needed with the Instapak® design, while 16 were needed with the previous solution. The foam packaging completely satisfied all involved at Stern Pinball. “I’ve been in customer service my whole life,” stated Blackwell. “Sealed Air analyzed my needs and used a consultative approach to create the perfect packaging solution for our pinball machines.” Blackwell added, “It’s the greatest thing we ever did.”
About Sealed Air
Sealed Air is a leading global manufacturer of a wide range of food and protective packaging materials and systems. Sealed Air’s widely recognized and respected brands include Bubble Wrap® cushioning, Cryovac® food packaging products, Jiffy® protective mailers and Instapak® foam-in-place packaging. The Company’s products protect and preserve its customers’ products from the plant or warehouse through the rigors of the distribution chain. Sealed Air’s industry-leading investment in research and development enables the Company to deliver innovative packaging solutions that add measurable value to its customers’ businesses around the world. For more information about Sealed Air, please visit the Company’s web site at http://www.sealedair.com/.
About Stern Pinball
Stern Pinball is the only coin-operated pinball manufacturer in the world. Since 1986, Stern Pinball has created and released pinball machines featuring numerous themes including Disney’s Pirates of the Caribbean, SPIDER-MAN™ and FAMILY GUY™. The company is based in Melrose Park, Ill. For more information about Stern Pinball, please visit the company’s web site at http://www.sternpinball.com/.
The pulse of the packaging community