Sealed Air Provides Protection for NASA Space Shuttle Transport
Last updated on
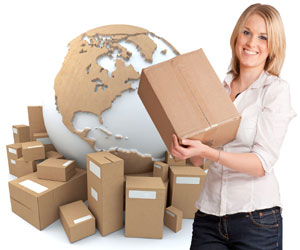
The protective packaging experts at Sealed Air are no strangers to challenging and sometimes extraordinary requests. Just four years ago they provided the materials and expertise to protect “Leonardo,” the most complete reticulated dinosaur fossil ever discovered. Naturally, they launched into action when contacted by NASA earlier this year – by officials familiar with their contribution to the dinosaur project – about the need for packaging design and materials to protect a valuable piece of U.S. Space Program history.
The Full Fuselage Trainer, or FFT, was a part of every Space Shuttle mission for the three decade duration of the shuttle program. As the name implies, the simulator was a full-size
training model designed to the same dimensions as an operational shuttle orbiter. Astronauts used the trainer for such exercises as learning how to exit the vehicle after emergency landings and to gain familiarity with the lighting inside the orbiter’s payload bay. The fully assembled FFT includes a crew compartment, replica payload bay (replicating the shuttle’s cargo area; this was separated into two sections, forward and aft, for shipment) and an aft section including three bell-shaped engine replicas and the vertical stabilizer (tail).
Constructed and housed at the Lyndon B. Johnson Space Center in Houston and used to train every Shuttle astronaut in the program’s history, the FFT was a part of 135 space missions yet never left the ground until its maiden flight aboard a specialized cargo plane in June 2012. After conclusion of the Space Shuttle program, NASA awarded the space-flown orbiters and the FFT to museums and attractions where they will be enjoyed by generations of visitors, with Seattle’s Museum of Flight selected to receive the FFT.
The journey to get the trainer to its new home in Seattle was complex, involving NASA officials, museum staff and packaging experts from Sealed Air. Getting all the FFT components from
point A to point B would require logistics for both ground and air transportation. The FFT’s three engine-bell replicas and other ancillary equipment were trucked to Seattle in wooden crates on a 52-foot long trailer in April of 2012. However, the remaining FFT components required an additional level of care, particularly for the 24-foot long, 17,000-pound crew compartment. This is where Sealed Air’s packaging experts came in.
“Our company takes pride in providing products and expertise that enable us to protect what’s important to our customers every day, and we consider it an honor to have been tasked with helping to preserve such a historically important object,” said Sean Kerins, Sealed Air Protective Packaging government sales manager and member of the FFT crew compartment project team.
Boldly Going Where No Packaging Has Gone Before
Sealed Air’s involvement in the FFT’s journey from Johnson Space Center to the Museum of Flight began soon after officials selected the mode of transportation. After considering and
rejecting several options, including water transport via barge, officials chose NASA’s Super Guppy, a plane specially designed to carry outsized cargo, as the preferred method of
transportation to Seattle.
Even as the preferred option, the airborne trek on the Super Guppy would provide its own challenges, with the necessary flight path adding an element of difficulty. The cargo aircraft, with the large, heavy FFT crew compartment aboard, is limited to low altitude and thus must navigate around the mountainous regions of the western United States rather than flying directly over the high ranges. This plan would take the Super Guppy through areas with the potential for summer storms that could cause turbulence much like that experienced by other cargo and passenger flights. Limited room to maneuver over or around such storms or other turbulent obstacles would require extra diligence in cushioning the FFT from potential movement and abuse.
Among the initial observations by the seven-member Sealed Air technical team working on the project were some unique characteristics of the FFT, particularly the crew compartment. In addition to its large size and weight, the structure includes a bottom with 60,000 square inches of surface area with no flat surfaces.
Such concerns were but a small step for the Sealed Air team used to making giant leaps in custom packaging solutions around the world on a daily basis.
“One of the hallmarks that sets us apart in the industry is our willingness to work with customers to create custom solutions,” said David Hagood, Sealed Air Protective Packaging technical lead.
“Our protective packaging solves unique shipping challenges every day. The primary difference in this situation is we are talking about an object of such historical value that it would be virtually impossible to put a price tag on it. Not to mention the unusually large size of the object.”
Hagood acknowledges the “wow factor” of such a high profile assignment, and compares this scenario to Sealed Air’s 2008 custom protective packaging solution developed to transport
Leonardo, a project to which he contributed.
“The challenge that must be solved in packaging to protect any object for transportation, whether it is a laptop computer shipping from the factory to a consumer, a 77-million year-old dinosaur fossil like ‘Leonardo’ or the trainer used to prepare Shuttle astronauts for missions outside of the Earth’s atmosphere, is to determine the appropriate material for the level of abuse the object could encounter during the journey to its final destination,” said Hagood.
Concerns such as space constraints inside the Super Guppy, weight and dimensions of the FFT components, abrasion tolerance, temperature, air pressure and other environmental factors during the trip, and many others, were involved in the team’s analysis. Sealed Air worked side by side with officials from both NASA and the Museum of Flight to assess the need and develop a custom solution and plan for implementation.
Houston, We Have Packaging Solutions
The packaging process took place at a facility close to Houston’s Ellington Field after the crew compartment was moved from the Johnson Space Center at the end of May 2012. In a two day period, working outside in temperatures consistently in the mid 90s, Sealed Air experts used nearly 2,400 pounds of Sealed Air Ethafoam® Synergy® fine cell polyethylene and Sealed Air Instapak® polyurethane foam to create the proper cushioning design to safely protect the trainer. 12-inch by 12-inch Ethafoam® Synergy® foam blocks were specially designed at Sealed Air’s Grand Prairie, Texas facility and were placed on a pre-fabricated grid to line the customized metal basket engineered by NASA to hold the trainer. After the blocks were positioned on the grid, two cranes lowered the trainer’s crew compartment into the basket and held it while the Sealed Air team spent the next several hours positioning the Instapak® GFlex® foam-in-place foam on the sides and back of the trainer. Instapak® foam was then added to fill any remaining voids and to protect the nose of the compartment. Preparing the two sections of the payload bay followed a similar process.
In total, the team used the following materials to protect the FFT’s crew compartment and forward and aft payload bay components during their flights aboard the NASA Super Guppy.
Crew Compartment
- 350 lbs of Ethafoam® Synergy® polyethylene foam
- 610 lbs of Instapak® polyurethane foam
Forward Payload Bay Section
- 300 lbs. of Ethafoam® Synergy® foam
- 360 lbs of Instapak® polyurethane foam
Aft Payload Bay Section
- 400 lbs of Ethafoam® Synergy® foam
- 360 lbs of Instapak® polyurethane foam
Hagood offers an interesting comparison.
“On the crew compartment alone, we used easily enough Instapak® foam to protect 1,000 laptop computers during shipment,” he said. “As for the Ethafoam® Synergy® foam, we used enough for 300 laptop packs.”
Hagood says the products used represent the appropriate amount to do the job, and demonstrate the lengths to which the Sealed Air team will go to develop solutions tailored to
individual customers’ needs. He says typical applications for Ethafoam® Synergy® foam include case inserts, tool control and automotive dunnage, while Instapak® foam has unique cushioning properties that protect a range of objects during shipping, warehousing or handling.
The Eagle Has Landed
“The FFT components arrived in excellent condition,” said Museum of Flight Public Relations Manager Ted Huetter. “We were able to remove the packaging and put the crew compartment on display in the Space Gallery the same day it arrived.”
Now safely transported from Houston to Seattle and being reassembled for permanent display in the 15,500 square foot Charles Simonyi Space Gallery at the Museum of Flight, the FFT
represents the only opportunity for citizens anywhere in the world to enter and tour a full-size Shuttle inside. This differs from display plans for the space-flown orbiters assigned to attractions in various other U.S. cities, which include only external viewing opportunities.
Back to the Future
In keeping with the Sealed Air commitment to sustainability, all the Sealed Air Ethafoam® and Instapak® foam used during the project was returned the company’s Grand Prairie and Fort Worth manufacturing facilities. The Ethafoam® material will be recycled via the company’s closed-loop recycling system, and the Instapak® foam will be processed at regional waste-to-energy facilities where it is converted into electricity for local communities.
Indiana Solo, or Han Jones?
With the project now complete and the FFT scheduled for reassembly in the Simonyi Gallery, Hagood can reflect on the diversity of unique protective packaging scenarios to which Sealed Air has contributed in a relatively short time period. He and his fellow Sealed Air Protective Packaging experts share experiences perhaps only the actor Harrison Ford could appreciate after having played both Indiana Jones and Han Solo.
“We’ve got to be the first and only company ever to protect both a pre-historic dinosaur fossil and a space program trainer for shipping to new destinations,” he said.
The pulse of the packaging community